Precision Plastics. Accelerated Delivery.
The intricacies of fabricating medical-grade molded components for today’s complex medical devices—precision at scale, regulatory compliance, and speed to market—pose significant challenges for OEMs. Viant turns these obstacles into opportunities with deep expertise, advanced capabilities, and a global supply chain, delivering solutions that ensure quality, optimize costs, and accelerate market entry.
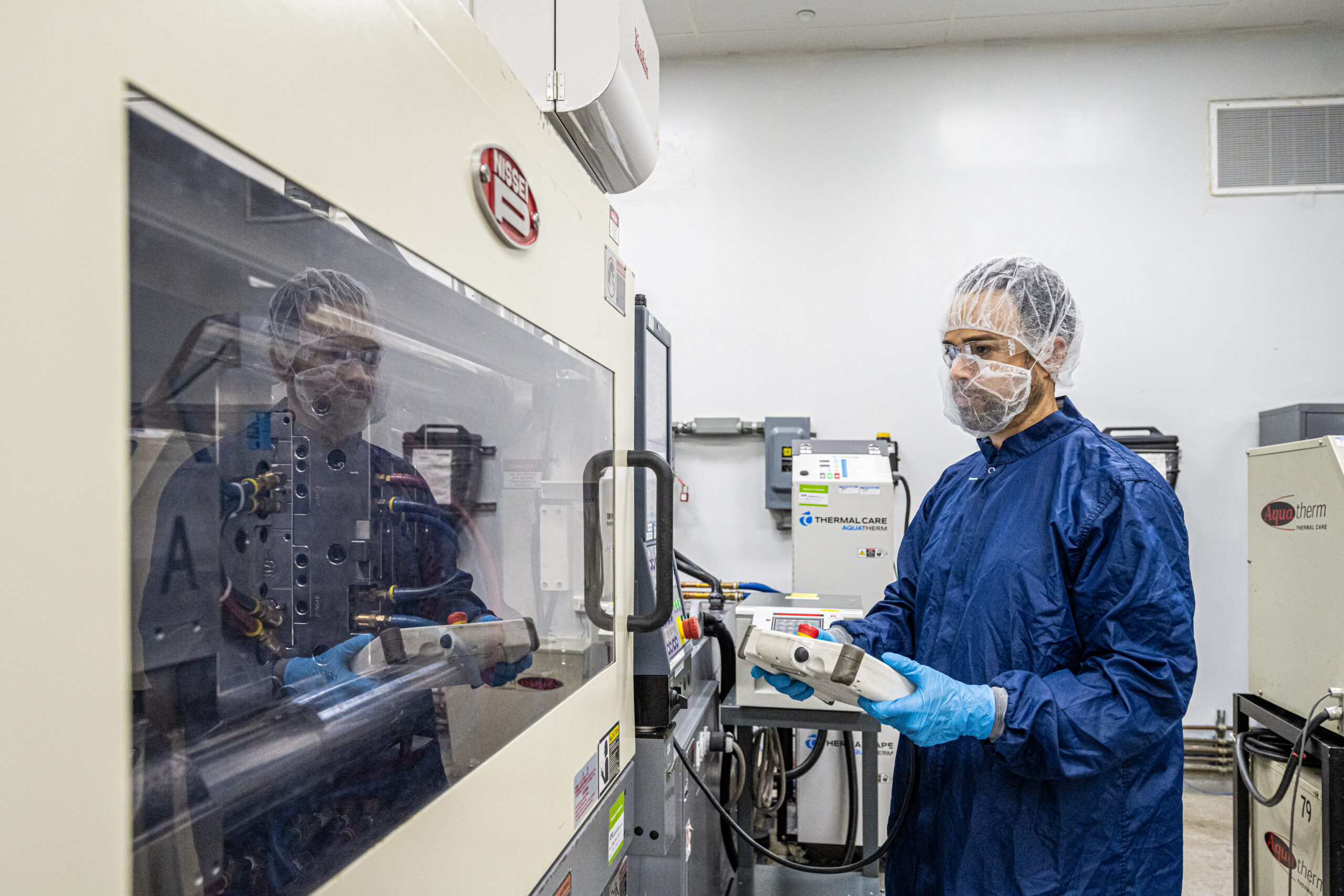
Your Partner for Medical-Grade Plastic Components
Precise performance at scale
Ensure your device performs optimally with high-precision components manufactured to exacting standards, even for your largest production runs.
Reliable cost optimization
Achieve predictable and competitive pricing through our vertically integrated efficiencies, optimized supply chains, and commitment to value-added engineering.
Speed to market
Accelerate your time-to-market and gain a competitive edge with our streamlined production, rapid prototyping, end-to-end control, and responsive project management.
Why work with Viant?
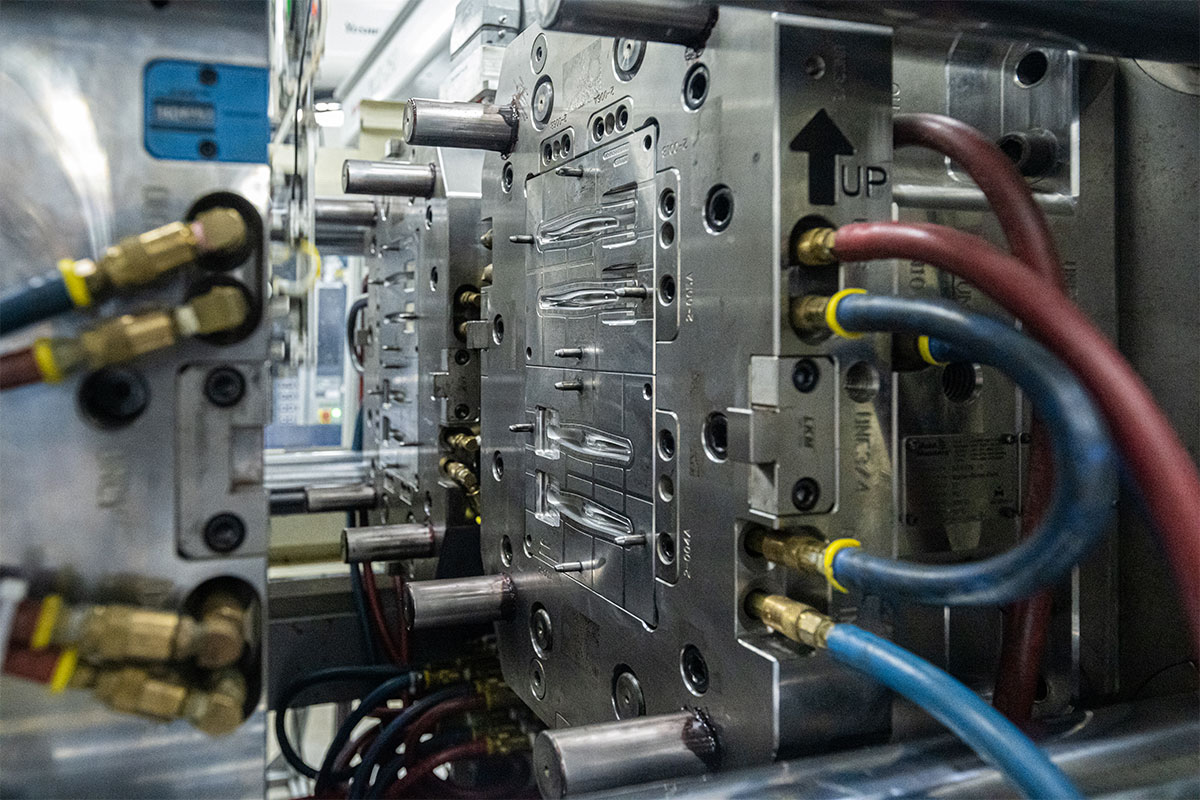
Pioneering plastics innovation
Integrate cutting-edge technologies, automation solutions, and materials into your device and turn our market-leading capabilities into your competitive advantages.
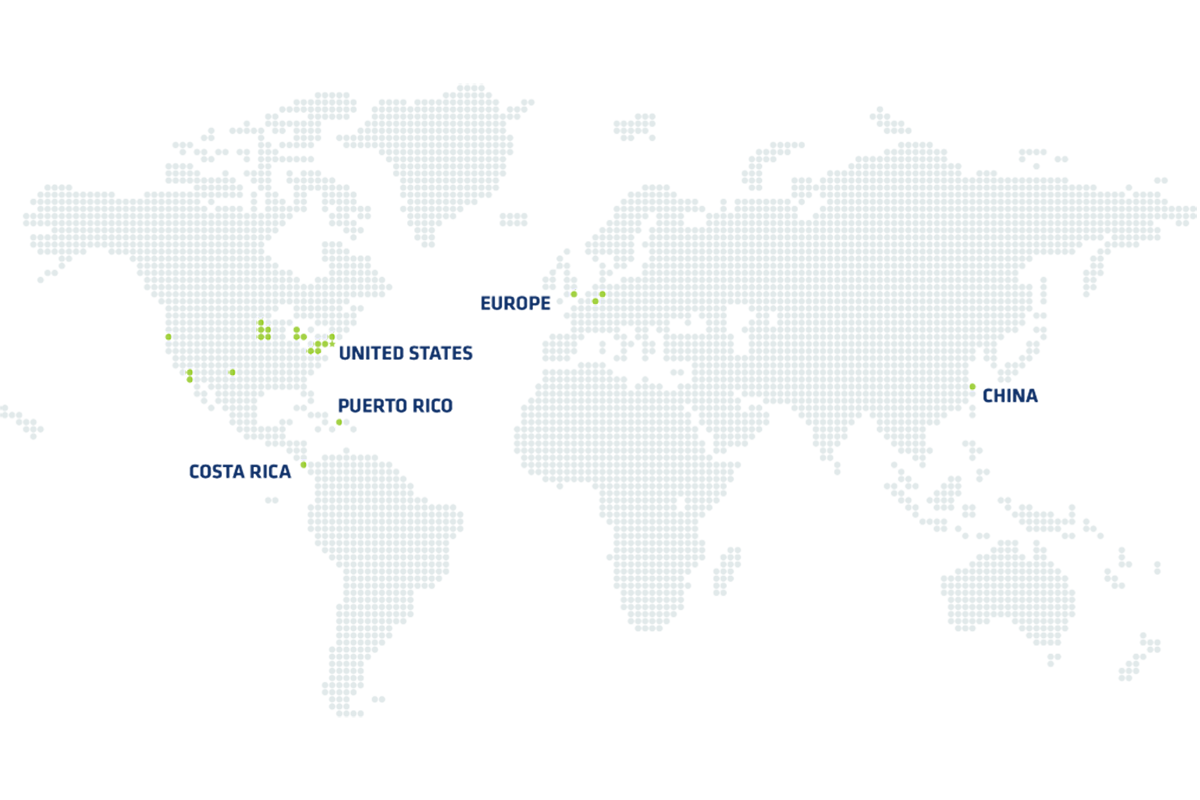
Global strength
Leverage our worldwide network of manufacturing facilities and technologically optimized supply chains to drive production efficiencies, reduce lead times, and ensure continuous availability.
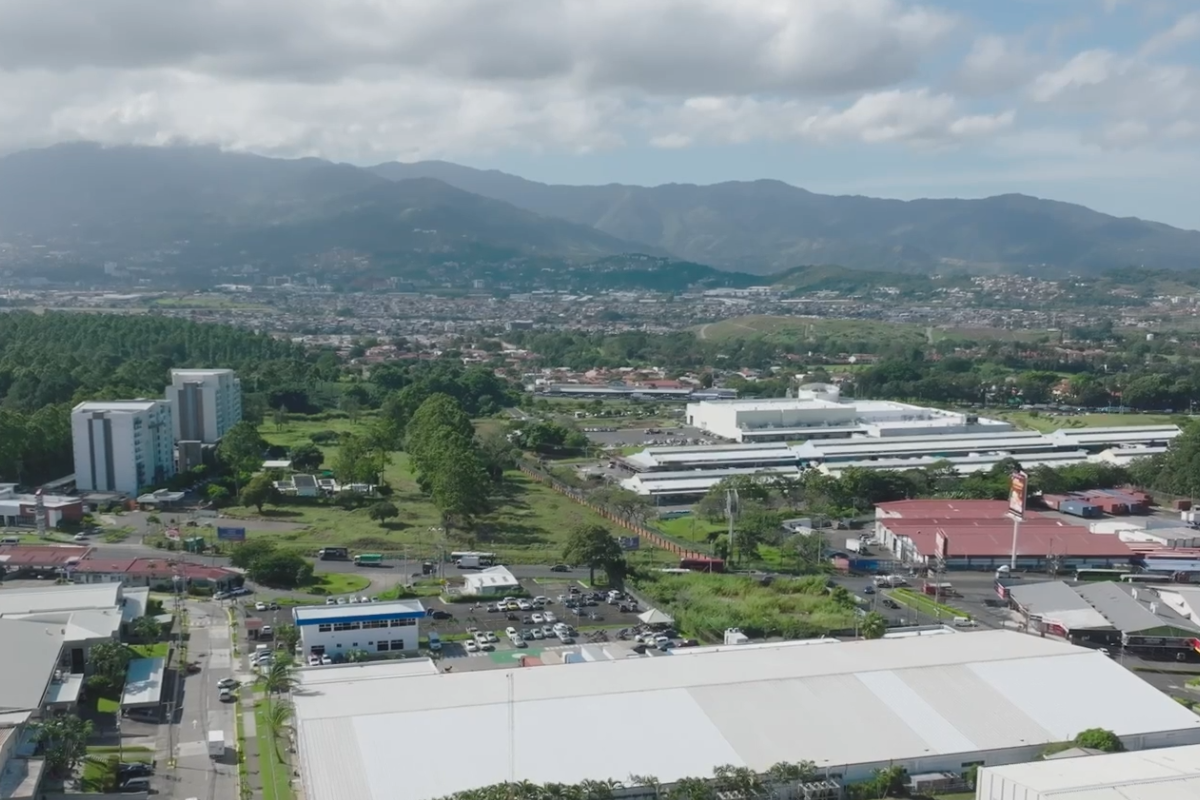
A sustainable business partner
Precision Molding Capabilities
Viant’s precision molding expertise spans a wide range of techniques and materials to meet the unique needs of your medical device:
Injection Molding
Mastering the intricacies of complex injection molding, we produce high-quality components with exceptional precision and repeatability. Our capabilities span low-high volume molding, including specialized processes such as insert molding, two-shot molding, over molding and high-temperature molding for demanding applications.
Micro-Molding
Material-Specific Molding
We possess deep expertise in processing a wide range of advanced materials, including commoditized materials like liquid silicone rubber (LSR) and thermoplastics in addition to highly engineered plastics. Leverage our expertise to achieve the specific performance characteristics required for your device.
High-Volume Production
Leveraging large-cavity molds and in-mold operations, we efficiently scale production to meet your high-volume demands while maintaining consistent quality and cost-effectiveness. Press side automation solutions further increase fabrication efficiency, enabling seamless integration with downstream processes. This results in reduced cycle times, minimized manual intervention, and enhanced productivity.
Specialized Processes
Our specialized processes, such as needle over-molding and 2-shot molding, enable the creation of complex geometries and multi-material components, expanding design possibilities and enhancing device functionality.
Precision Plastics for Critical Medical Devices
From life-saving drug delivery systems to advanced surgical instruments and diagnostic tools, Viant’s precision molding expertise supports a wide range of clinical applications.
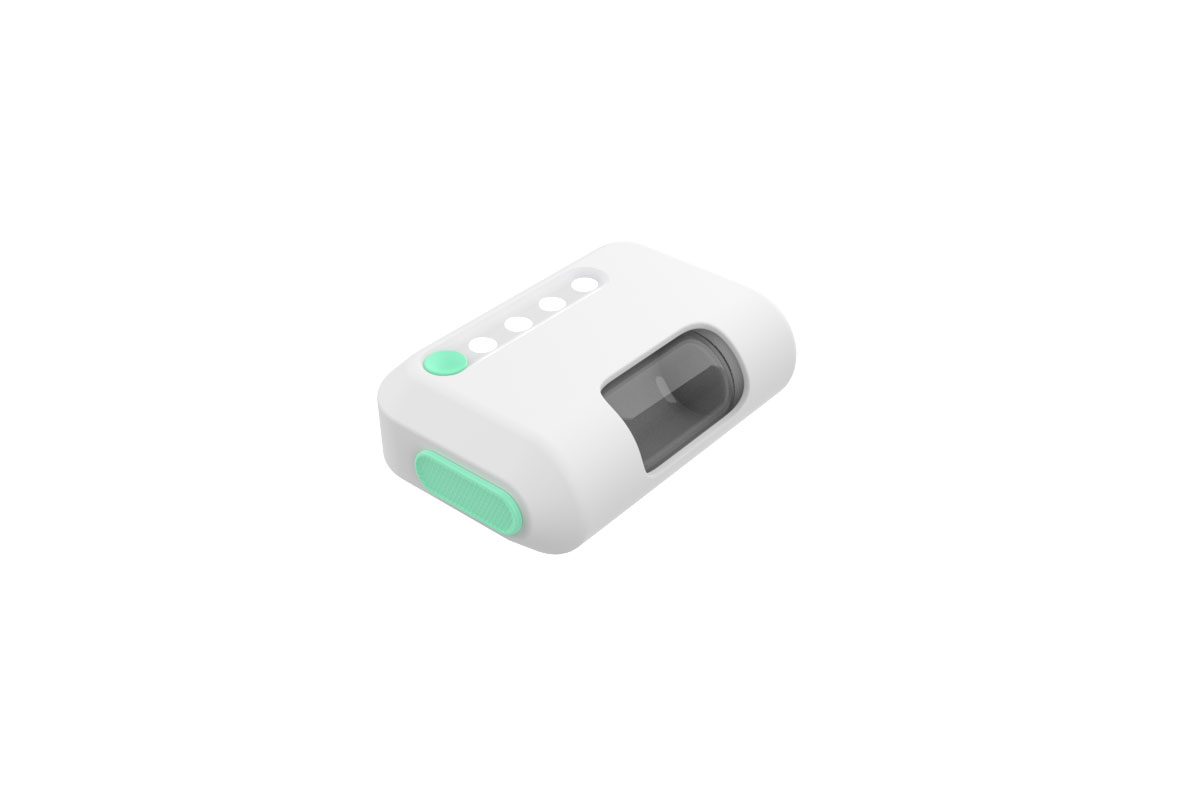
Drug Delivery
Producing critical components for drug delivery systems such as auto-injectors, insulin pumps, and inhalers, ensuring precise dosage and reliable performance.
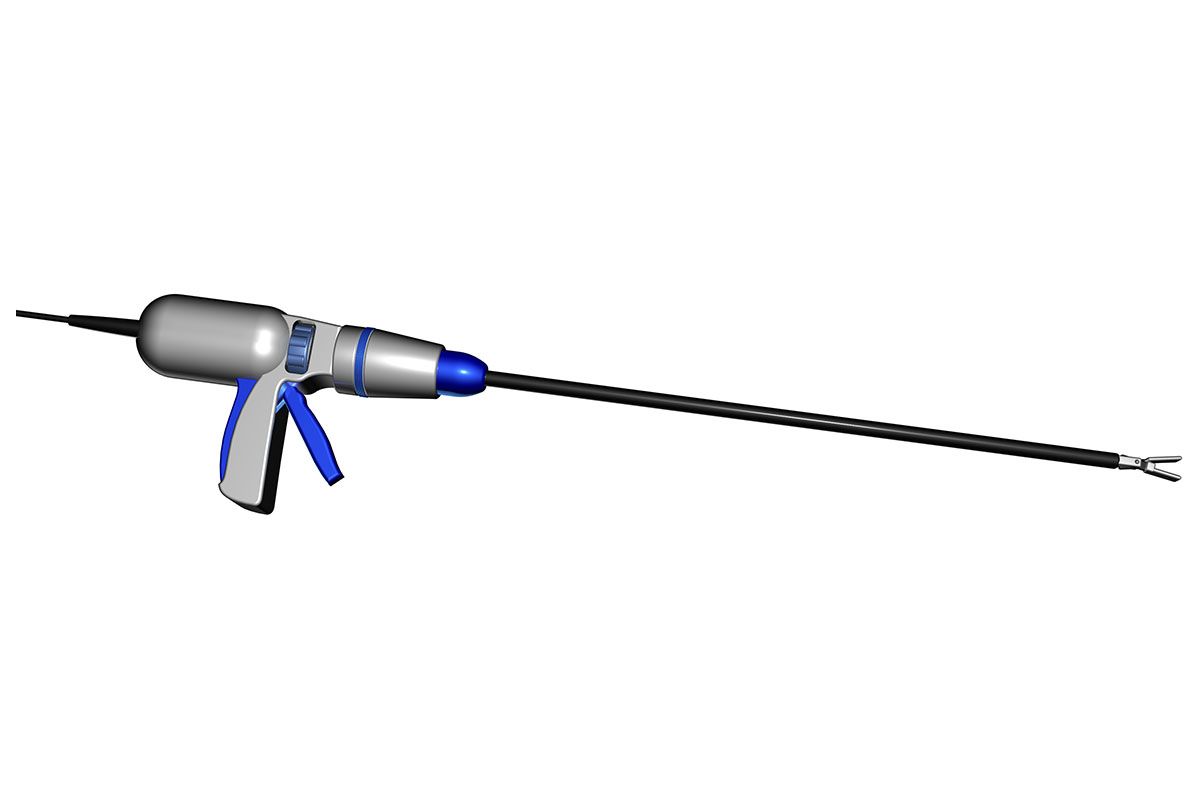
Surgical Instruments
Production of intricate components for surgical instruments, including handles, ablation devices, and minimally invasive tools.
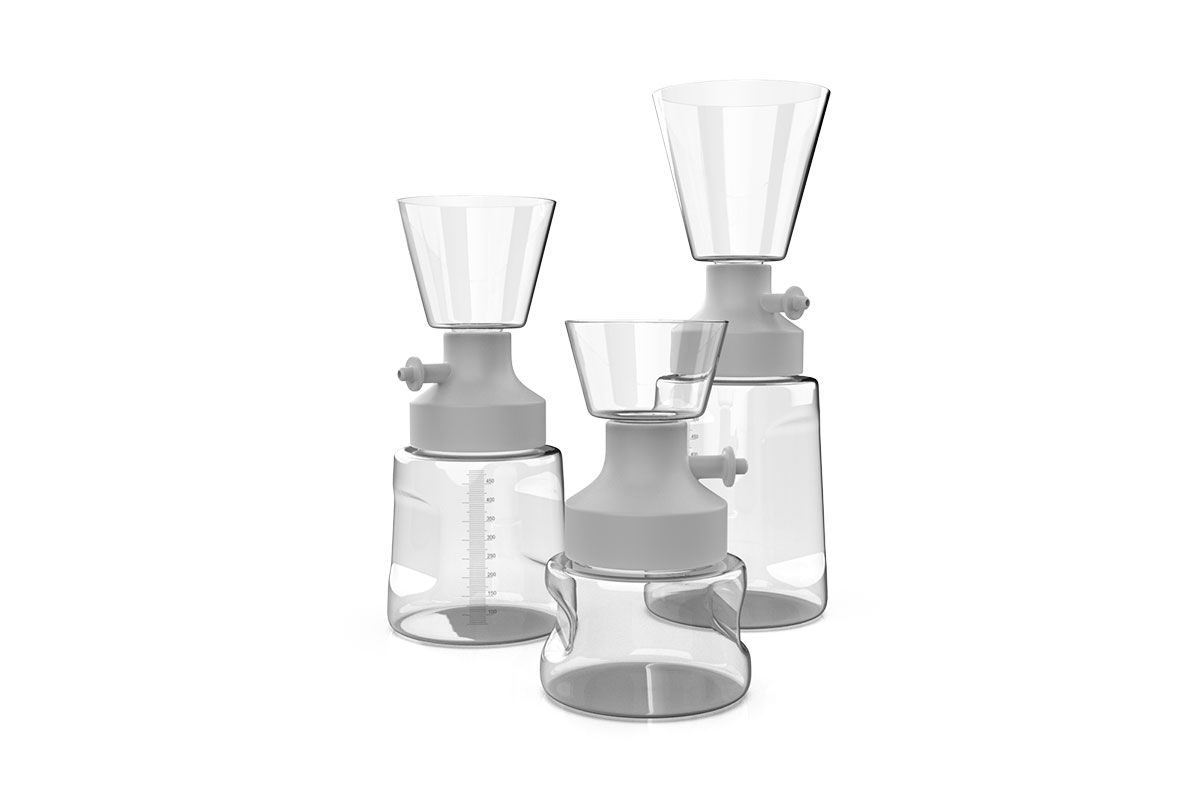
Laboratory & Diagnostic Equipment
Manufacturing high-quality plastic components for diagnostic equipment, such as lab testing components, blood testing vessels, and filtration devices.
Scaling at Speed
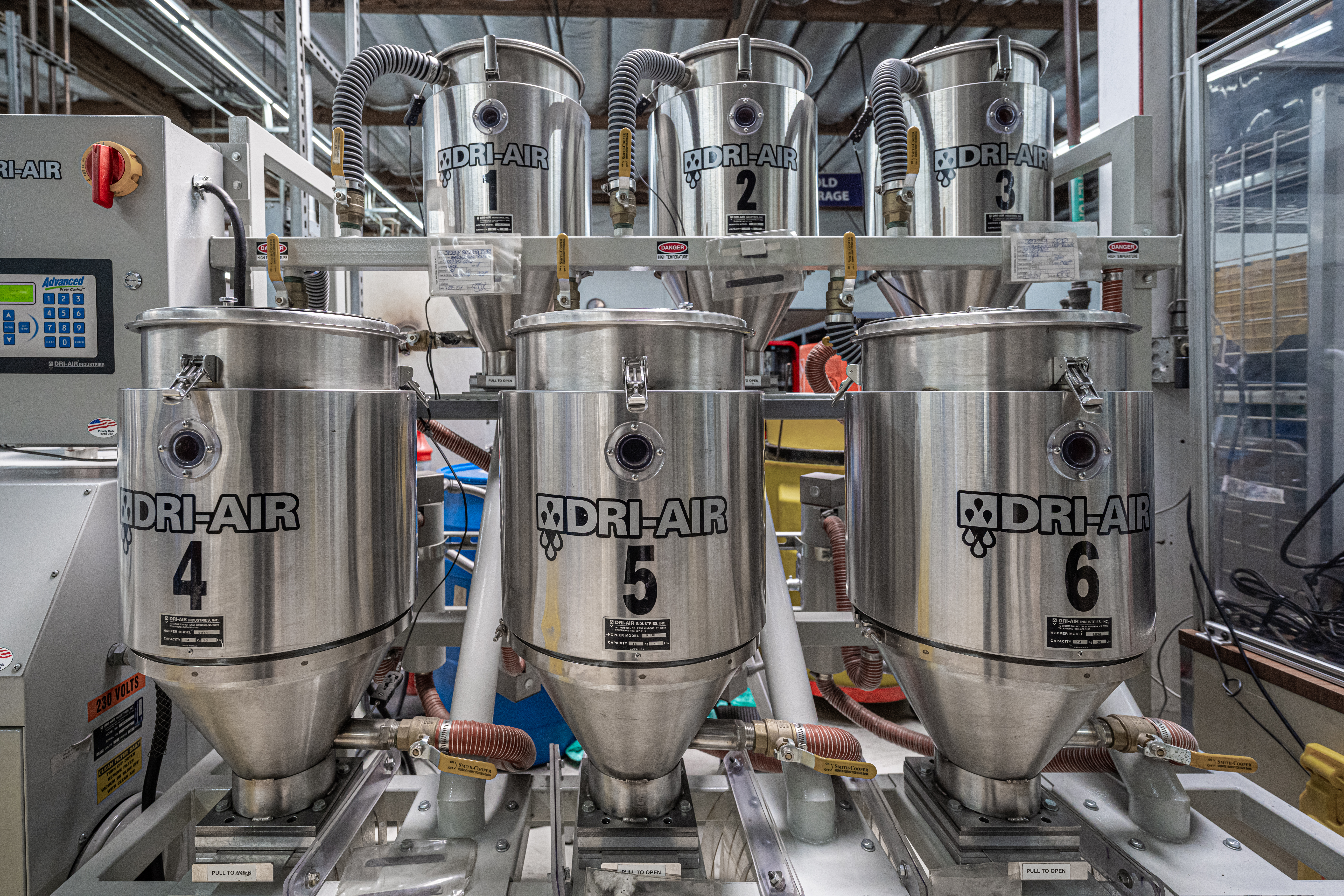
case study
Novel retooling & automation boost production to meet 30% demand growth—in just 13 months.
Facing unprecedented demand, a medical device manufacturer partnered with Viant to overhaul their supply chain and rapidly increase production of its transformative automated injection system. The result? A 20% decrease in cycle time, a 50% reduction in scrap rate, and a 13-month turnaround — half the industry average — bringing these life-changing devices to more people.
The Viant Difference
Leading Technologies
- Advanced Injection Molding: Utilizing decoupled molding techniques and scientific molding principles and process monitoring technology to optimize process parameters, ensuring consistent quality and repeatability.
- Next-Gen Automation: Leveraging state-of-the-art automation and robotics to increase efficiency, reduce costs, and ensure precision.
- In-House Tooling: Global Tooling team designs and builds high-performance molds in-house, allowing for tighter control over quality, lead times, and costs.
Uncompromising Quality
- Quality for Life Philosophy: A culture of ownership, accountability, and continuous improvement to ensure the highest standards.
- Robust Quality Systems: Aligned with ISO 13485, FDA regulations, and risk management best practices to deliver consistent compliance and audit readiness.
- Measured Excellence: Leveraging critical quality metrics to mitigate risk, improve processes, and maintain customer trust in every component.
Broad & Deep Expertise
- Experienced Engineers: Extensive experience in medical device plastics, providing expert guidance on design, material selection, and process optimization.
- Material Science Expertise: Deep understanding of the properties and applications of various medical-grade plastics ensures the optimal material is selected for your device.
- Dedicated Program Management: Providing proactive communication and support throughout your project, ensuring a smooth and successful outcome.
Ready to discuss your project?
See how Viant’s complete plastics portfolio can help you achieve exceptional quality, accelerate your time to market, and optimize your device costs.