THE CATALYST FOR YOUR NEXT INNOVATION
Proven expertise and engineering ingenuity—from initial concept to market success.
Viant’s unique approach to medical device design & development delivers the high-touch, high-energy experience of working with a specialized, agile design firm—while giving you the confidence of a proven innovation partner that has helped to successfully engineer and launch some of the most advanced medical devices on the market today.
We combine our industry-leading technical capabilities with decades of real-world experience and relentless ingenuity to break through barriers and accelerate your product development at any stage, while connecting you to global manufacturing capabilities to seamlessly move through design transfer and into full-speed, full-scale production.
Move your innovation forward today.
Value-added engineering
An agile, flexible approach to partnership
From global medical device OEMs to early-stage innovators bringing new ideas to life, we provide a unique a la carte approach plugging in anywhere (or everywhere) in your development lifecycle. This allows us to fill resource gaps, problem-solve to break through barriers, and find smart ways to add clinical value and manufacturing efficiency to your design. These enhancements help differentiate your device and drive commercial success.
Feasibility
Feasibility
- Voice of Customer / User Requirements
- Product Specifications
- Concept Ideation
- Concept Assessment
Design
Design
- Rapid Prototyping
- DFM / DFA / DFx
- Full DHF Generation
- Packaging Design
- Test Method Development
Verification
Verification
- 3P
- Risk Analysis
- Design Documentation
- Design Verification
- Testing
Validation
Validation
- Design Validation
- Component / Supplier Qualification
- Process / Sterilization Validation
- Regulatory Submittals
Design Transfer
Design Transfer
- Device Master Record
- Production Ramp
- Lean Production Process
- Continuous Improvement
- Program Initiation
Scalable Manufacturing
Scalable Manufacturing
- Small Batch Manufacturing
- Vertical Integration
- Automation Expertise
- Flexible Manufacturing System (FMS)
- Lean Manufacturing
- Outsourced Assembly & Packaging
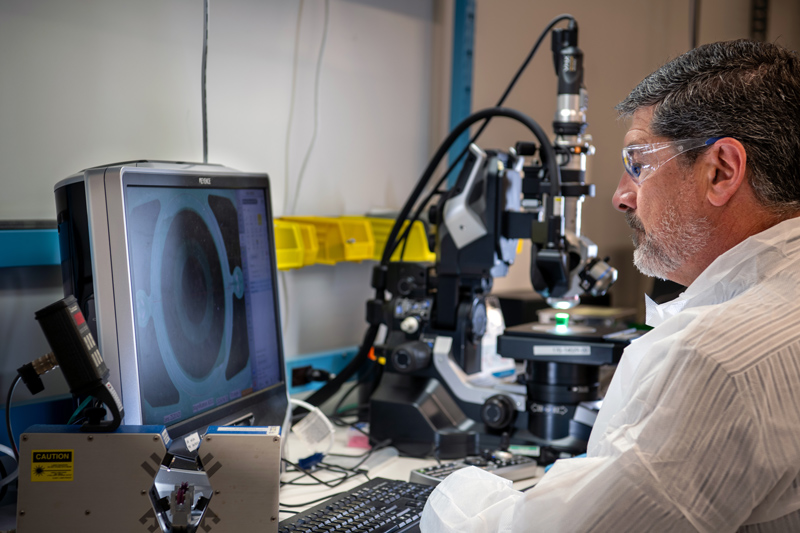
The energy of a startup
We bring aggressive ingenuity and an anything-is-possible mentality to help you innovate, incubate, iterate and keep your ideas moving forward. Our energetic problem-solving brings infectious momentum to your project—at any stage.
Bring your ideas to life.
Industry-leading clinical & technical expertise
Our renowned team of design and development engineers are behind some of the most innovative devices in orthopedics, bioelectronics, robotics, minimally invasive surgery (MIS), and more, bringing industry-leading expertise in materials, coatings, simulations and bioengineering. Together, we help customers redefine what’s possible in medical diagnostics and treatment.
Add world-class engineers to your team—on demand.
Viant Technical Capability Highlights:
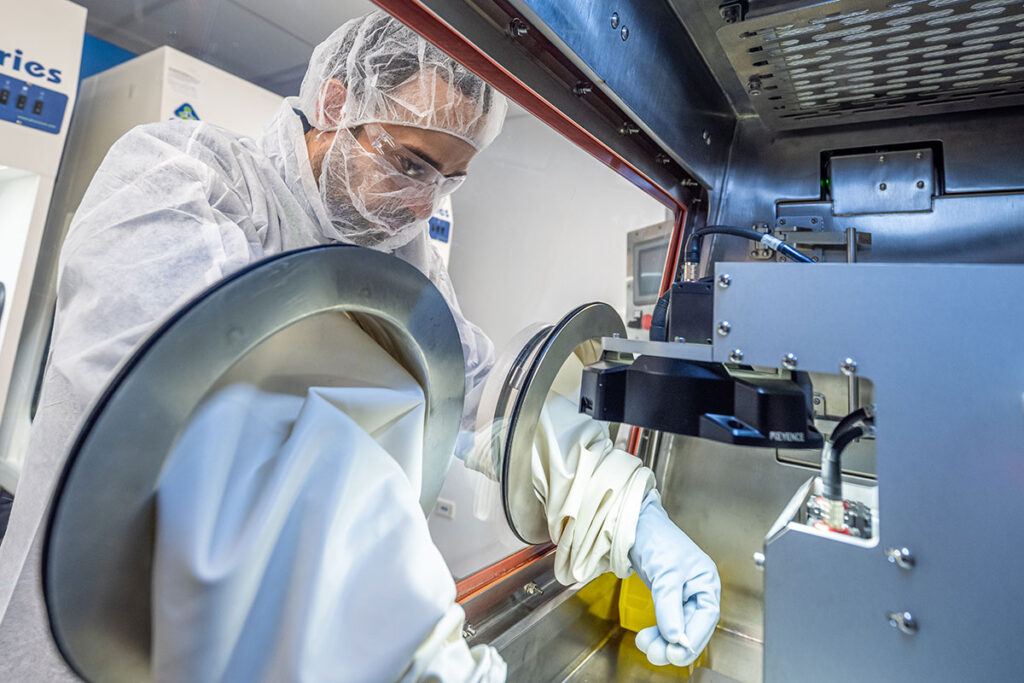
A legacy of proven success
Behind our D&D team’s startup energy is a proven track record of turning ideas into commercial products and transforming IP into market value for customers. With a team of 100 creative problem solvers, we manage over 60 active projects and commercialize an average of 5 programs per year. Our proven success gives your project an advantage from the start, and decades of real-world experience help guide your project to market faster.
Our experience gives you an edge.
Accelerate speed to market
the scale & speed of a global manufacturing leader
Design & Development success stories
See our innovation and expertise in action
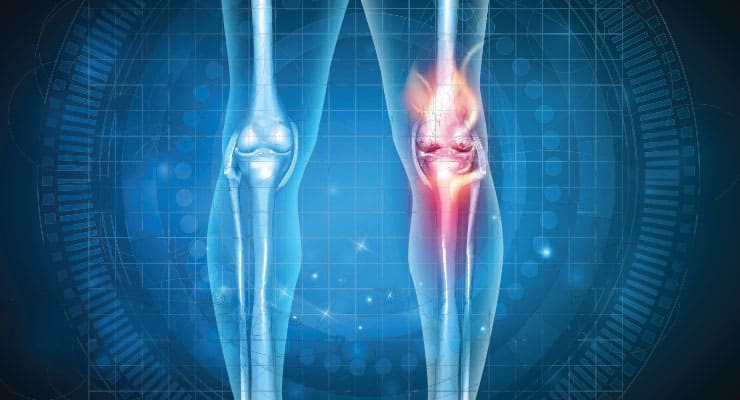
Innovative Design & End-to-End Capabilities Help Reduce Complexity & Boost Efficiency for Orthopedic Instrument System
Expertise in hybrid materials makes complex designs more efficient and sparks an award-winning design.
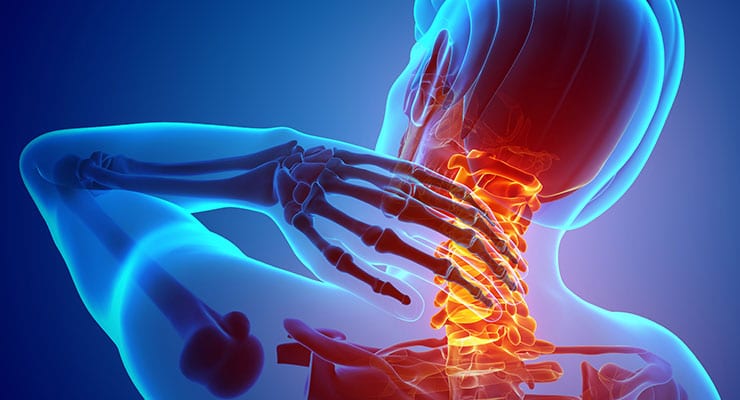
Vertical Integration Speeds Scale-up for US Launch of Orthopedic Implant
Single-source supply and end-to-end solutions guide major improvements to production capabilities and create efficiencies for a European medical device manufacturer.

Design, Manufacturing & Supply Chain Expertise Fuels Stability and Growth of Arthroscopic Product Line
Vertical integration, material insourcing, automation, lean manufacturing, and scrap reduction lead to a market-leading artificial cervical disc.